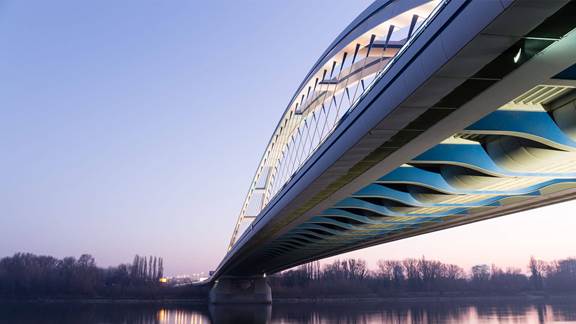
General industry
Heating processes are common in industrial manufacturing. Induction heating is often the preferred choice.
Introduction
Efficient and reliable production is critical for industries all over the world. Unplanned downtime or unexpected quality defects can quickly turn expected gains into massive losses. As induction technology is accurate, controllable, fast and repeatable, more and more industries choose induction heating over other heating alternatives such as gas. In addition, induction heating does not emit carbon dioxide and eliminates naked flames.
- Mobile induction heating for general tasks
- Stationary induction heating for specific tasks
.jpg?mw=640&mh=1024)
Aviation
Product quality and process consistency are obviously crucial to the aviation industry. That is why the accurate, repeatable and contact-free induction heating has become so popular with aircraft manufacturers, airlines and their suppliers.
Typical applications:
- Induction brazing of fan blades and blades for casings
- Induction brazing of various parts for fuel systems, e.g. fuel connections
- Induction brazing of various components in hydraulic systems
- Postheating of welding repairs such as in casings for jet engines
Railway
The unrivalled accuracy, control and efficiency of induction heating makes it ideal for key tasks in the manufacture and maintenance of rolling stock and rails.
Typical applications:
- Shrink-fitting of lock rings, ball bearings, brake pad centre hubs, steel tyres on rims, wheels on shafts, loctite connections,
- Pre-heating of rails
- Hardening of rails and hubs
- Welding of rails in field
Oil and gas
ENRX has been helping oil and gas service companies since the mid 1990s.
Typical applications:
- Post Weld Heat Treatment
- Pre Weld Heat Treatment
- Pre-heating before coating
- Tube bending
- Soldering
- Shrink fitting of bolts and nuts, steam valves, bearings, hubs, gears, sprockets, impellers, ompressors and retaining rings
- Removal of rubber coatings and glued parts
- Hardening of spray coatings
- Straightening
Shipbuilding
ENRX provide induction heating equipment that is used in ship yards around the world for the construction, repair and maintenance of all kinds of vessels.
Typical applications are:
- Deck and bulkhead straightening during construction
- Straight welding of beams in double hulls
- Paint and coating removal
- Brazing of copper components
- Hardening of large gears, winches and chains
- Heat treatment of shafts
- Pre-heating of valves prior to welding
Metal and foundry
Our very first induction equipment items were designed and built for the metal and foundry industry. Over the past five decades, we have led the way in developing time and money saving solutions for this sector.
Typical applications:
- Forging of billet heaters and horizontal/vertical bar end heaters
- Melting of metal and glass
- Plasma heating of titanium and silicon
Wire and cable
The unrivalled accuracy, control and efficiency of induction heating makes it ideal for many key tasks in the manufacture and processing of wire and cable products.
Typical applications:
- Drying post cleaning or removing water or solvent from coatings
- Curing of liquid or powder based coatings. Providing a superior bond strength and surface finish
- Diffusion of metallic coating
- Pre heating for extrusion of polymer and metallic coatings
- Heat treatment including: stress relieving, tempering, annealing, bright annealing, hardening, patenting etc.
- Pre-heating for hot-forming or forging, especially important for specification alloys
Image gallery
-
The coating removal system is a game-changer that facilitates removal of coatings from carbon steel, structural steel and other metal substrates.
-
Induction coating removal outperforms traditional methods. No blast media. Safer, healthier working conditions. Easy clean-up of paint and coating debris. Up to 90% time-saving.
-
ENRX has worked closely with customers across the globe to develop the coating removal system.
-
The coating removal system is compact, light-weight and easy to move around worksites.
-
Much easier clean-up. The coating material peels off in flakes rather tan being pulverised.
-
Induction brazing steel support bars for sofas.
-
Induction brazing of a microphone.
-
Automated, high-output solutions for bar end and partial heating.
-
An ENRX CHV vertical heater. Capable of heating any type of profile, including preformed components, the CHV supports manual and robot loading.
-
A heated workpiece being ejected from a CBB horizontal heater. The CBB ejects parts in a single location – a major benefit for operators.
-
Designing unique, customised bar end solutions is an ENRX strength. Our technical capabilities let us meet virtually any customer-specific requirements.
-
ENRX bar end and partial heaters are field-proven systems used by many manufacturers around the world. Each system is backed by the resources and service capabilities of ENRX.
-
A new 1.200 kilo-capacity single-axis tilting furnace being installed at a bearing manufacturer’s facility.
-
An ENRX induction furnace at work. This graphite crucible contains molten brass.
-
FIB is our range of single-axis tilting furnaces. The FIB coreless (shown here) features an innovative coil design that maximises efficiency.
-
ENRX furnaces maximise productivity and product quality. For example, the dedicated crucibles in moving coil furnaces eliminate inter-alloy contamination.
-
Induction melting is a process where metal is melted into liquid form in an induction furnace’s crucible. The molten metal is then poured from the crucible, usually into a cast.
-
Induction heating is a smart and proven way of melting metal and glass.
-
Induction heating is characterized by features that make it ideal for offshore-related tasks: flameless, precise, mobile and versatile.
-
A Sinac being used to heat treat oil and gas pipelines
-
Motor house: A semi-automated system with integrated conveyor belt for easy integration in p
-
A proven solution in a tough environment. An ENRX PWHT unit in use on advanced, corrosion-resistant alloy pipe in the Sahara deset.
-
Mobile Minac systems bring induction solutions to offshore platforms
-
An operator replaces a bearing that has been heated with an ENRX mobile Minac system
-
The “Safe Concordia” accommodation and support platform. A mobile ENRX Minac system was used to pre-heat the weld area during the welding of a patch onto a crane tower.
-
An example of induction pre-heating: the pipe is being heated prior to receiving an anti-corrosive coating.
-
An induction coil specially designed and built for offshore industry requirements. Once heated by the coil (in red) the pipe can receive an anti-corrosion covering.
-
ENRX systems have been used for hot tap welding on the bed of the North Sea: Photo: Technip Norge AS.
-
Specialist coils being tested for the Tampen subsea hot tapping procjet. Photo: Technip Norge AS
-
An medium-frequency ENRX Sinac pre-heats seamless offshore pipe prior to coating.
-
No dust, no fumes, no noise. An ENRX heater gets to grips with 170 mm anode stubs.
-
Induction heating is increasingly used to remove the giant nuts and bolts in power stations’ turbines.
-
ENRX designs and builds specialised systems for steel strip and wire and cable pre-heating.
-
Minac units are frequently flown to oil platforms to perform repairs and maintenance.
-
Shrink-fitting of main shaft bearings and sleeve rings.
-
Shrink-fitting of rotor shaft and motor-housing
-
Disassembling and shrink-fitting bearing and lock rings.
-
Bearing rings can be heated in a completely uniform manner and removed while the shaft remains cold.
-
The innovative ENRX shrink-fitting system can heat any size of motor housing for electrical motors and pumps.
-
More and more automotive sub-contractors are opting for induction heating to shrink-fit gear wheels
-
Induction heating used for changing the shafts of an old bridge
-
Shrink fitting with flexible cable
-
Disassembling and assembling of bearing rings at a railway repair shop.
-
Manual solution for shrink-fitting of motor house
-
Motor house: A fully automated system with robot handling.
-
Motor house: A semi-automated system with manual loading and unloading.
-
ENRX has delivered numerous solutions for shrink-fitting of stator housings.
-
Induction heating is widely used to straighten ship decks and bulkheads.
-
Induction straightening of heavy goods vehicles.
-
An ENRX Terac system ensures failsafe operation—it makes it impossible to overheat magnetic steel.
-
Terac works just as well on bulkheads and other vertical structures as it does on decks.
-
For added ergonomic comfort, the handheld transformer can be attached to a balancer and suspended from a magnet or wire rope.
-
Operators can work with Terac within a 45m radius of the base unit. An optional extension unit lengthens the work area to 60m radius.
-
ENRX Terac systems are specially designed for ship straightening. Each Terac includes a frequency converter, cooling system, operator panel and deck-heating unit.
-
Note the easy-to-use controls placed on the handle. It usually takes only a couple of hours to train an operator to use the Terac system.
Get in touch
Are you looking for support or product information, please contact us here