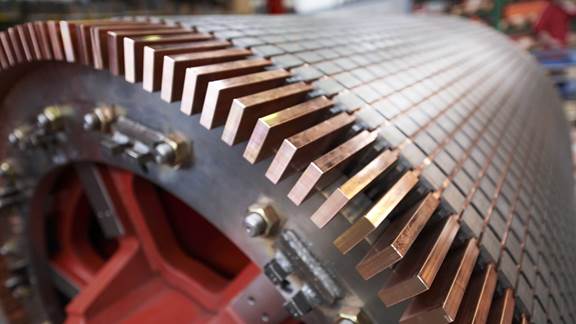
Induction brazing
ENRX offers brazing in various fields, such as the automotive, aviation, electrotechnical and white goods industries.
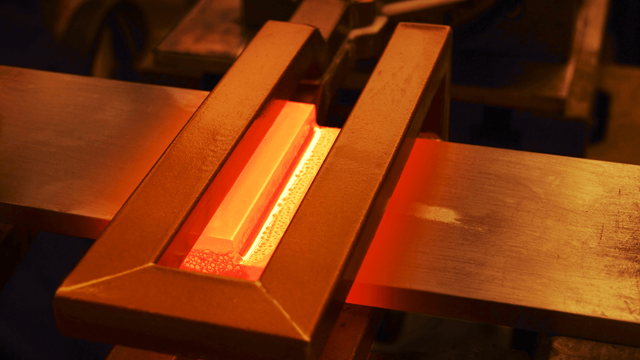
What is induction brazing?
Brazing is a materials joining process that uses a filler metal (and usually an anti-oxidizing solvent called flux) to join two pieces of close-fitting metal together without melting the base materials. Instead, induced heat melts the filler, which is then drawn into the base materials by capillary action.
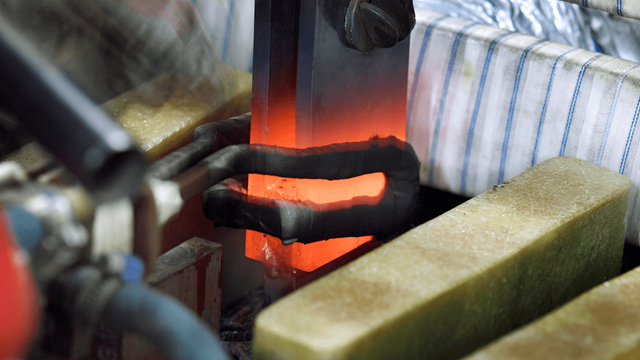
What are the benefits?
- Join a wide range of metals, even ferrous to non-ferrous
- Heat only narrowly defined areas
- Ideal for integration into production lines
- Correctly brazed joints are strong, leakproof and corrosion resistant
- They are also very neat, usually requiring no further milling, grinding or finishing
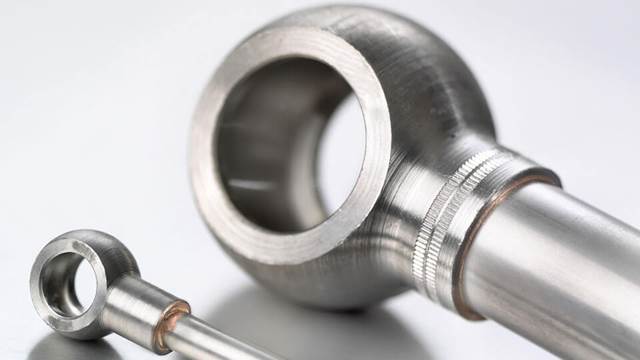
Where is it used?
ENRX brazing systems can be used for virtually any brazing task. To date, our systems are typically used in the electrotechnical industry to braze generator and transfomer components like bars, strands, rings, wires and SC-rings. They also braze fuel pipes as wellas AC and brake parts for the automotive industry.The aeronautics sector uses induction to braze fan blades, blades for casings, and fuel and hydraulic systems. In the houseware industry our systems braze compressor components, heating elements and faucets.
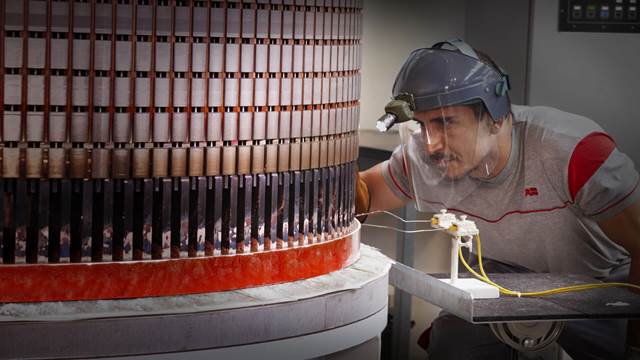
What equipment is available?Â
Our brazing solutions usually include an ENRX mobile Minac or stationary Sinac system. Both product families offer a wide range of output powers and frequencies, together with automatic matching and robot compatibility.
related products
related industries