Struggling with high electricity bills?
“We can help!”, says Grzegorz Korzuszek. The Managing Director of ENRX Poland wants tube and pipe producers caught in the energy crunch to see how high-quality impeders can cut power consumption.
During the lockdown of 2020, we saw a lower-than-normal demand for electricity, gas and coal, but last year’s economic recovery greatly increased energy consumption and sent prices skyrocketing. In parts of Europe, the wholesale price for electricity more than tripled in 2021, reaching the highest level in decades. In fact, some say this record-breaking surge in energy prices threatens to derail the whole post-pandemic economic recovery and even slow down the transition to a more sustainable production.
One industry segment that has to battle the soaring energy costs is the tube and pipe producers.
“Unfortunately, we can’t do anything about the price of electricity, but, with our high-quality impeders, we can definitely help you cut your power consumption”, says Grzegorz Korzuszek. “After raw materials, energy is always the main cost to anyone in the tube and pipe industry”, he points out. “So, don’t let that energy go to waste by using poor quality impeders and inductors!”
The Managing Director of ENRX Poland sees the energy crunch from another perspective as customers are looking to become more energy-efficient by improving their production process and investing in new machines.
“We’re obviously happy about this”, he says, “but we also want to tell all tube and pipe producers that we have an excellent product that will them help cut their electricity costs, namely our impeders.”
Impeders are an integral and critical component in the pipe welding process. Often neglected, they can cost your business substantial amounts of money if they are not properly designed and manufactured, and correctly selected. Unfortunately, producers often opt to save money on impeders, thinking there is minimal difference between the best and the not-so-good. However, that is not the case.
“Do you know that not having the correct ferrite length can increase welding power consumption by thirty percent?”, Grzegorz asks. “That quickly becomes an expensive way to save a few Euros.”
A good impeder will effectively increase the impedance of the parasitic current path around the inside circumference of the pipe, ensuring the power is directed into the weld vee. In addition, it concentrates the magnetic flux created in the work coil, so that a more energy is induced into the pipe.
The design and placement of the impeder can drastically affect the efficiency of the weld. Impeders from ENRX EHE have the highest quality ferrite grade to give optimum efficiency and stability during the production process.
“A major producer in Turkey actually reported €28,000 annual energy savings on five tube mills after changing to our HR4B ferrite cores”, Grzegorz says. “Another one of our customers reduced welding power consumption by 15 percent after installing a large diameter rectangular cluster impeder system on a 24” pipe mill”, he continues. “In this case, that was a massive 225 kW!”
The life expectancy of impeders must also be taken into account when trying to keep costs down. Usually, the time it takes to change one costs considerably more than the impeder itself, so durability is important.
“We all know that downtime can be hugely expensive, so our impeders are built to last”, Grzegorz assures us. “The ferrites are protected by the best available casings, ensuring effective cooling, resistance to mechanical damage and good thermal endurance.”
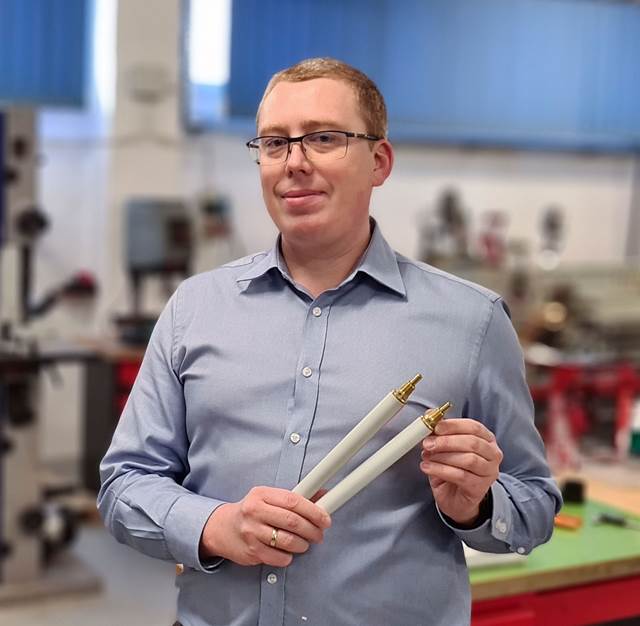
Grzegorz Korzuszek, Managing Director of ENRX Poland .