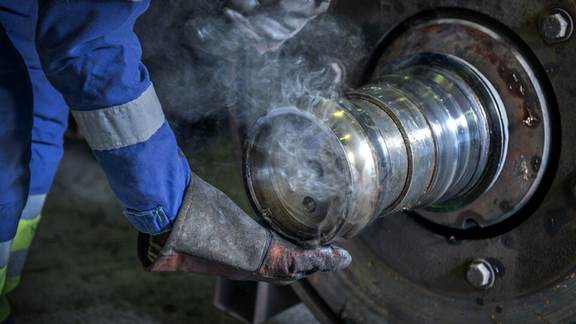
Shrink fitting
Induction shrink-fitting uses thermal expansion to fit or remove parts made of metal. By employing controlled heating, this method takes advantage of the expansion and contraction of materials, ensuring a precise and secure assembly or disassembly process.
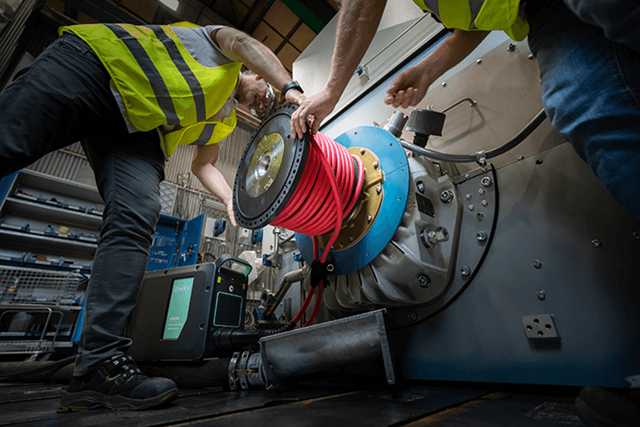
ENRX rental solutions are ideal for:
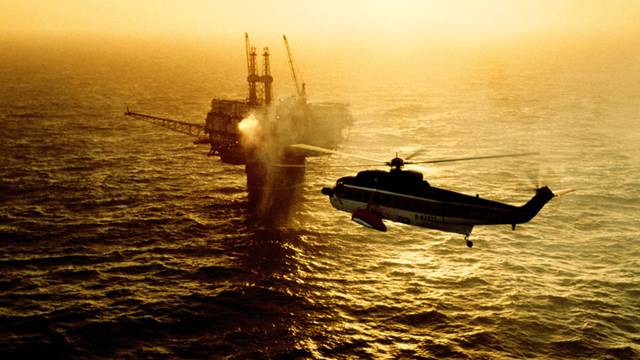
Fly in. Fix. Fly out.
Adair Swan and his colleagues at Rolls-Royce had a problem. They wanted to carry out maintenance work on a Rolls-Royce gas generator located on a BP rig in the North Sea.
It was clear that heat would be needed to remove the various components—thrust collar, auxiliary gear, coupling hub—attached to the generator’s power turbine shaft. But because the generator was located in a designated hazard zone, any use of open flames such as a gas torch would shut down production. Naturally keen to avoid a costly shutdown, Swan contacted ENRX UK to see if induction heating could be used. Jon Philpott of ENRX tells what happened next. “Our first job was to show we could meet the stringent safety standards set by Rolls-Royce and BP for on-platform heating. To do this we organized a successful workshop trial of our equipment. BP and Rolls-Royce then asked for an offshore trial on a redundant package of the Bruce platform.”
Located 380 km northeast of Aberdeen on the Scottish east coast, the Bruce Field is one of the largest gas/condensate (light oil) fields in production in the UK North Sea. Plans for the on-site trial were moving ahead when fate dramatically intervened. Jon explains: “Just before the planned offshore trial there was an unscheduled shutdown of a power turbine rotor on the Bruce platform. Our equipment and an ENRX engineer were rushed to the rig to heat and remove the turbine’s thrust collar, auxiliary gear and coupling hub from the turbine rotor. Once a new rotor was installed, the engineer used induction heating to reassemble the components.”
Induction: the new standard
The emergency intervention by ENRX on the Bruce Platform was a great success. In fact, according to Rolls-Royce, the use of ENRX “resulted in the work being completed early and production restored several days ahead of schedule.” But the story doesn’t end there. Due to the proven success of the Bruce Platform project, induction heating has been adopted as the preferred method for removing/reassembling thrust collars, auxiliary gears and coupling hubs on almost all Rolls-Royce power turbines in operation in the North Sea. Other platform operators, too, are gradually phasing out costly open flame methods in favor of induction heating. The Bruce Platform project was one in a series of breakthroughs for ENRX in the North Sea.
Says Philpott in conclusion: “It was great to be trusted by such well-known companies as BP and Rolls-Royce. It was a vindication of everything we’ve been saying about induction heating—its speed, mobility, controllability and safety. But it was also great to be nominated for a BP Helios Partnership award.”
The award referred to by Philpott is a prestigious recognition by BP of external partners ‘delivering over and beyond what is expected contractually, demonstrating true team spirit.’
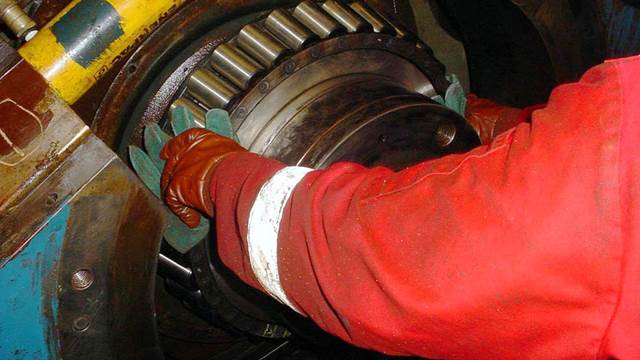
Using induction to shrink-fit components on a North Sea platform.
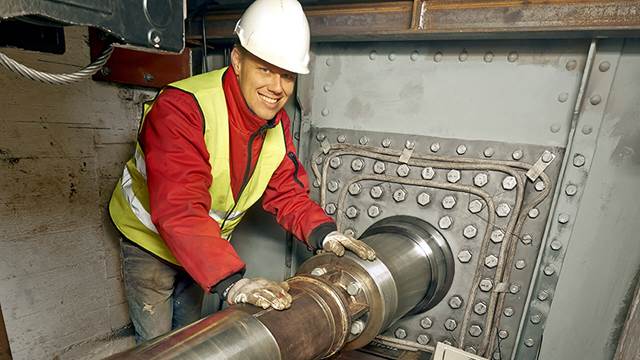
ENRX expertise used for bridge repair
ENRX Norway has fixed a local historical bridge. The bridge was built in 1957 and is equipped with two motors. Both of these were changed in 2010, however, the bearing and shaft were still the original ones from 1957. The bearings were now worn out and had to be replaced. The four shafts were also to be changed. Each shaft weighed 1,6 tons and measures 1,5 meters. The bridge is 224 meters long and each bridge flap 22 meters long.
JHS Engineering was responsible for the bridge repairs. They had planned on using nitrogen to cool down the connection points. However, calculations showed that this would be pretty expensive and the results uncertain. "We chose to contact ENRX to see if heating the connection ring by induction would be a better solution. It proves to be an excellent and perfect choice," says Project Manager in JHS Engineering, Atle Sigurdsen. JHS Engineering worked closely together with ENRX on the bridge and was impressed with what they experienced.
Terje Solgaard, Sales Manager ENRX, explains that the holes which the shafts are fastened to, are a little bit smaller than the diameter of the shaft.
"We had to make sure that the heating was quick, repeatable and accurate. We knew all the time that this task was meant for induction" emphasizes Solgaard and adds that he never doubted that ENRX would succeed.
"We held our breath when the first shaft was put in place. It fitted perfectly. If we had failed, it would have caused us huge delays in the project and the opening of the bridge" says a happy customer.
Application examples
Our shrink-fitting equipment
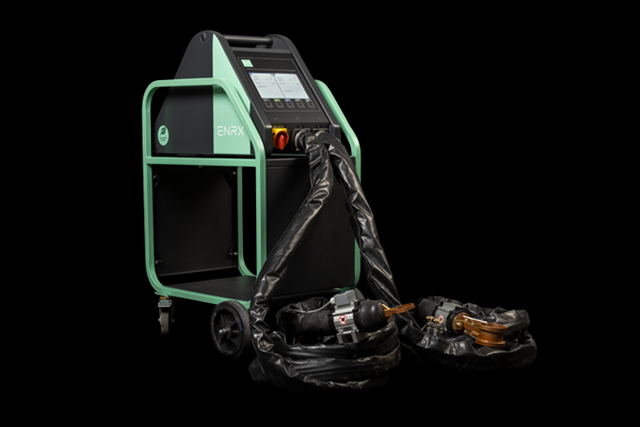
Minac
Minac is our family of mobile and versatile induction equipment. Examples of ideal jobs are brazing, curing, hardening, shrink-fitting and straightening.
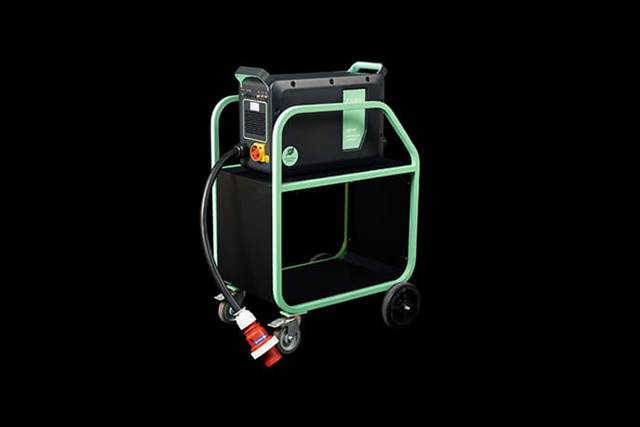
Ventac
Ventac is a portable air-cooled induction heating system that combines high continuous output (25 or 50 kW) with small size and low weight (only 36 kg). It has a sophisticated temperature control system that lets you stay in charge of your induction heating process. You get the task done quickly and can easily continue with the next one.