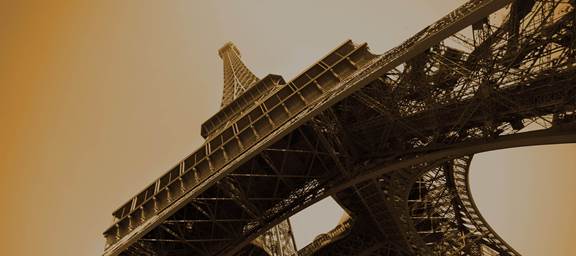
If it were today,would Gustave Eiffelhave used induction?
Two million five hundred thousand rivets. 18 038 metal parts to be joined together. One visionary engineer with a mission to create an outstanding landmark and engineering achievement. Just imagine if he would have had access to modern induction heating technology.
Masters of metal construction
In 1884, Gustave Eiffel’s company, Eiffel et Cie, was one of France’s most successful metal construction companies. They designed and built viaducts, bridges, and railway stations and were even selected to finish the design of the Statue of Liberty, thanks to Eiffel’s experience in handling wind stresses.
At this time, Eiffel’s two principal engineers, Émile Nouguier and Maurice Koechlin, came up with a fascinating idea: To build the world’s tallest tower, a 300-meter-high metal construction, for the upcoming World’s Fair of 1889. Together with Stephen Sauvestre, the head of Eiffel et Cie’s architectural department, they worked out an astounding design that gained Eiffel’s approval.
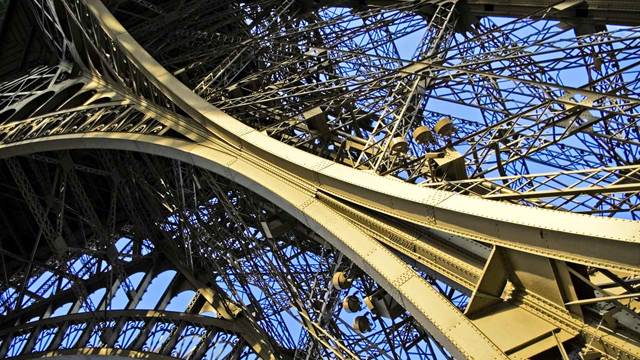
Functional beauty
However, not all liked the idea of a gigantic metal structure in the middle of Paris. Some meant it would not be possible to build at all, saying it was designed for looks and not for stability. Others, including 300 Parisian artists and writers, thought it would overshadow the beauty of the Notre Dame, the Arc de Triomphe, and the Louvre. To the sceptics, Eiffel said, “Is it not true that the very conditions which give strength also conform to the hidden rules of harmony?” and as history proves, it was Eiffel who got the last word.
The design has been examined again and again to understand why it was so successful, even long after Gustave Eiffel’s demise. The most recent is a 2004 investigation that concluded that the main mathematical principle of design is a non-linear integral equation based on counteracting forces between the wind pressure on any point of the tower and the tension between the construction elements at that point.
Shrink-fit, 1880’s style
The 18 038 wrought iron construction details that constitute 7 300 tonnes of the tower’s total weight of 10 100 tonnes are all held together by rivets, mounted with a method that was very refined at the time of construction.
The pieces were assembled using bolts at Eiffel’s factory in the suburb Levallois-Perret and then transported to the construction site. During assembly on site, the bolts were replaced one by one with rivets. Four men were needed to assemble each rivet – one to heat it, another to hold it in place, a third to shape the head and a fourth to beat it with a sledgehammer. After assembly, during cooling, the rivets contracted to give a very tight fit.
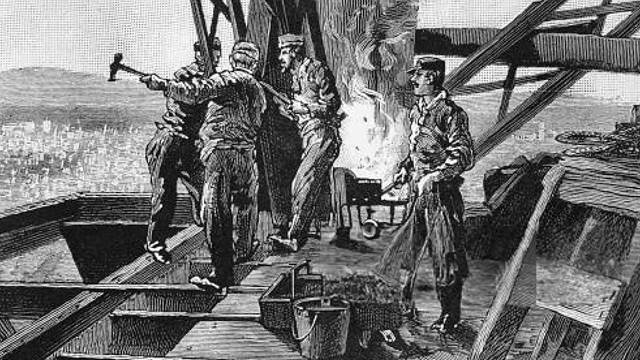
During assembly on site, the bolts were replaced one by one with rivets. Four men were needed to assemble each rivet – one to heat it, another to hold it in place, a third to shape the head and a fourth to beat it with a sledgehammer.
What if Eiffel had induction heating?
Would Eiffel have used induction heating if it was available? No one knows, but as he was a visionary, entrepreneur, and innovative engineer, we think he probably would. There would be no fuming coal forges, just controlled and efficient heating that could have turbocharged the entire operation. The benefits are mind-blowing – faster riveting, reduced staffing, and, most importantly, stronger joints. With its ability to deliver consistent and localised heat, induction heating could have elevated the Eiffel Tower’s structural integrity to new heights.
Not only would rivet assembly have been faster and easier, but induction heating could have made it possible to choose even more efficient and precise types of welding and joining. It could also have been used for heat treatment to enhance the mechanical properties of metal components, for metal bending and forming of intricate parts of the tower, and for constructing specialised components, ensuring they meet specific metallurgical requirements and tolerances.