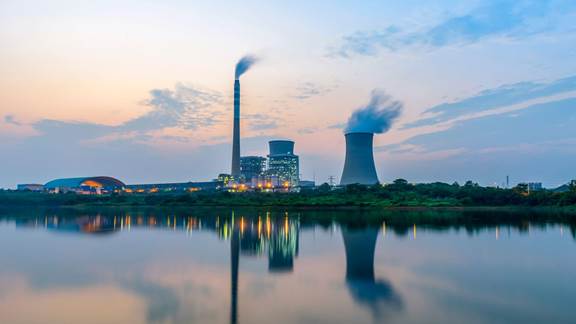
Bolt expansion
The use of induction heating for bolt expansion in high-pressure turbines is a powerful business tool. It is faster than resistance and flame heating, and its rapid, precise and localized heat doesn’t damage bolts and threads.
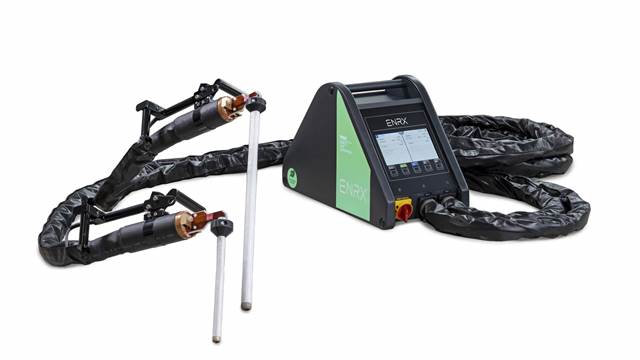
Bolt heating solution
The ENRX bolt expansion solution is built around a small yet powerful mobile Minac converter and specially designed inductor coils.
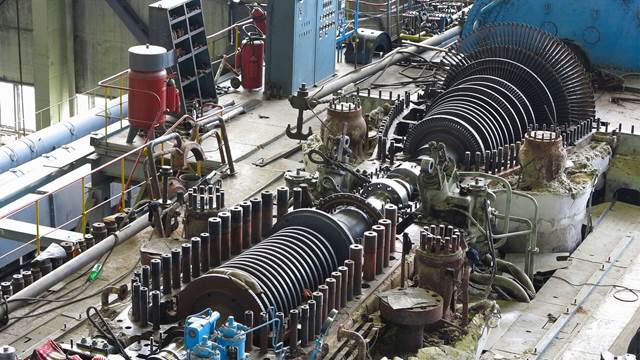
The nuts and bolts of better business
How two customers fared when they turned to ENRX to solve their bolt heating challenges.
British Energy, the largest electricity producer in the UK, utilises induction heating for bolt expansion. Fred Hunter, Development Engineer at British Energy’s Turbine Support Group, comments: “We used to rely upon resistance heaters to release the studs on turbine control valves. But it was far from an efficient procedure. Such technology is inherently unreliable. The electrical elements are fragile, fuses are prone to blowing, and it is essential to have a huge spares inventory on-site. Moreover, such heaters are not mobile. You can imagine the considerable prep-work that was needed before we could deploy the equipment.”
The limitations of resistance heaters had serious implications for British Energy. Opening control valves for inspection is a statutory obligation. That is, it is a legally mandated maintenance action—it has to be done. Since the frequency of such mandatory outages cannot be changed, the only cost-cutting opportunity lies in reducing the duration—and the knock-on disruption—of each outage. Converting to ENRX’s mobile Minac converters let British Energy achieve reductions in the duration of these maintenance
activities.
From days to hours
“That’s correct,” agrees Richard Stewart, Engineering Group Head at the Turbine Support Group. “We were very impressed when we ran our first trials with Minac. Previously, bolt loosening at one of our power plants took up to two days. Minac slashed that time to a couple of hours.”
The main reason for the time saving is Minac’s extremely quick and precise heat delivery. With gas or resistance heaters, excessive heat is entered into the workpiece and heating times are slow. During re-assembly, lengthy periods are spent waiting for the assembly to cool down prior to measuring the bolt strains.
“The ENRX method,” adds Stewart, “lets us better deliver the right amount to just the right place, leading to considerably shorter cool-down times. Minac is now part of the standard
maintenance kit used by our Group at three British Energy power stations.”
The conversion from resistance to induction was a relatively painless experience. “There were the inevitable teething hitches, one of which was a high starting current that caused tripping. But the ENRX guys worked with us and they fixed the problem by adding an additional transformer.”
Shorter outages are not the only benefits delivered by Minac. Because the Minac equipment is mobile and so easy to use, British Energy’s own in-house maintenance staff—in this case its Turbine Support Group— can now perform the bolt loosening and tightening. The procedure was formerly outsourced to external subcontractors with induction heating expertise. “This,” says Stewart, “of course means we have complete control. We can undertake our maintenance actions as needed during outages. This flexibility means that sub-contractors are not kept waiting on-site, thereby minimising costs.”
75% faster
Obviously, Minac can be used outside of power stations for bolt loosening applications. One prime example of the versatility of Minac is the case of Sulzer Elbar B.V., part of Sulzer Turbo Services. Based in Lomm in The Netherlands, Sulzer Elbar specializes in gas and steam turbine refurbishment, component manufacture and field service and gas turbine relocation. The company also offers inventory management and maintenance service agreements. Previously, Sulzer Elbar used a gas bolt heater. But according to Rob Bormans, loosening one bolt took on average 12 minutes. So when Bjørn Røsvik, an ENRX application engineer, organized a demonstration of Minac, Bormans and his colleagues were “absolutely impressed” when “bolts were loosened in a record time of only three minutes per bolt.”
Røsvik is deservedly thrilled with the outcome of the work together with Sulzer Elbar: “This case really illustrates the potential of Minac for this demanding application", he says. "Thankfully, it seems more and more companies—especially those concerned about costs and quality—are realizing that they don’t have to continue with outmoded gas and inefficient resistance heaters. Induction is a viable, proven alternative.”
Røsvik first demonstrated Minac to Sulzer Elbar more than one year ago. Since then cooperation has developed, and the company has acquired two Minacs, a Minac 50–80, and a 25–40 model. Comments Bormans in conclusion: “I’m sure we will find new applications within our company for induction heating. I’m happy for Sulzer Elbar that we chose the right partner for solving our bolt heating problems!”
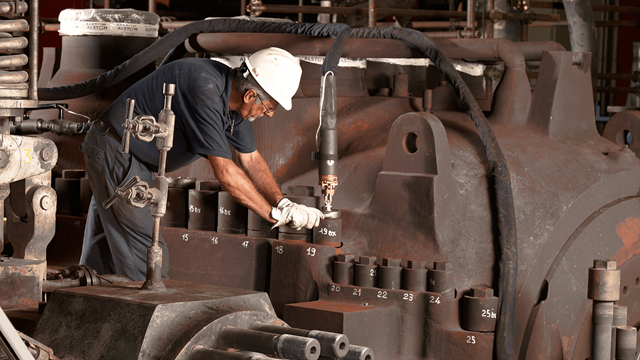
The Italian job
Venice, home to Piazza San Marco, the Rialto Bridge... and a rather interesting bolt expansion job on a steam turbine.
The canals and architectural splendour of Venice make it easy to forget it is also a large modern city, a place that around a quarter of a million people call home. And that’s not counting the tourists, 50,000 of whom clog the waterways and piazzas every day. Then there are the city’s surrounding industrial areas. Nearby Porto Marghera, for example, is one of Italy’s most important chemical processing centers.
All the above means a reliable power generation and distribution system is essential. And with any critical system, it is vital to keep scheduled downtime to a minimum. This is particularly true for turbines, as even a few hours of unplanned outage can result in major revenue losses. The time pressure facing service engineers is made even worse by the technology traditionally used to expand and remove the large bolts that secure turbine covers.
Alessandro Mariani of ENRX Italy explains: “Open flames and resistance heaters have serious drawbacks. The former method is slow, uncomfortable and inaccurate— and there’s a risk of excessive heat input damaging the threads. The latter has reliability issues, with a risk of rods melting inside the bolts. So when Alstom Power in Italy was performing planned maintenance on a turbine in Marghera just outside Venice, they asked us if induction heating was a viable alternative.”
Mariani continues: “We held a demo in Milan for Alstom where we showed how our mobile Minac systems, complete with special elongated coils, are perfect for bolt expansion. We covered a lot of ground; even explaining the benefits of a Minac ‘Twin’. This is a single converter connected to two independent handheld transformers. One operator can work on two bolts at the same time—in effect doubling his productivity. Or two operators can work simultaneously, each with their own transformer.”
Alstom were sufficiently impressed that they ordered two Minac 25/40 systems. Although the outer dimensions of each Minac is only 345 x 708 x 453mm, the system’s handheld transformer delivers a maximum output power of 40kW. When using a Minac, the heating process is so quick there simply isn’t time for heat to travel into the thread area. And thanks to electronic controls, key process parameters such as temperatures, ramp-up and dwell times can be set in advance and repeated with amazing accuracy.
According to Mariani, Alstom were delighted with Minac's performance in Venice. "Sure, the job was completed much faster than it would have taken had traditional methods been used. No damage was caused to nuts or bolts. And the operators really appreciated Minac's comfort and safety. In short, nothing unexpected happened. Minac did what it does best—it got the job done."